Teenage Engineering’s new K.O. II sampler is like a grown-up version of its Pocket Operator series, crossed with a 1970s/80s-era calculator. It’s getting musicians so excited that it sold out in days, and it offers features that are utterly unique in the world of hardware samplers. But maybe even more interesting than the device itself is the way it was designed and built.
Instead of creating another synth out of custom parts, Swedish musical instrument maker Teenage Engineering grabbed boxes and boxes of off-the-shelf parts, and then worked out how they could build a new sampler. And then they designed a factory to do it.
“One project was to build a production line from scratch, all in house. And the other side was to build a synth,” TE founder and head of hardware David Eriksson told iFixit over Zoom. “And we did it in parallel, same team.”
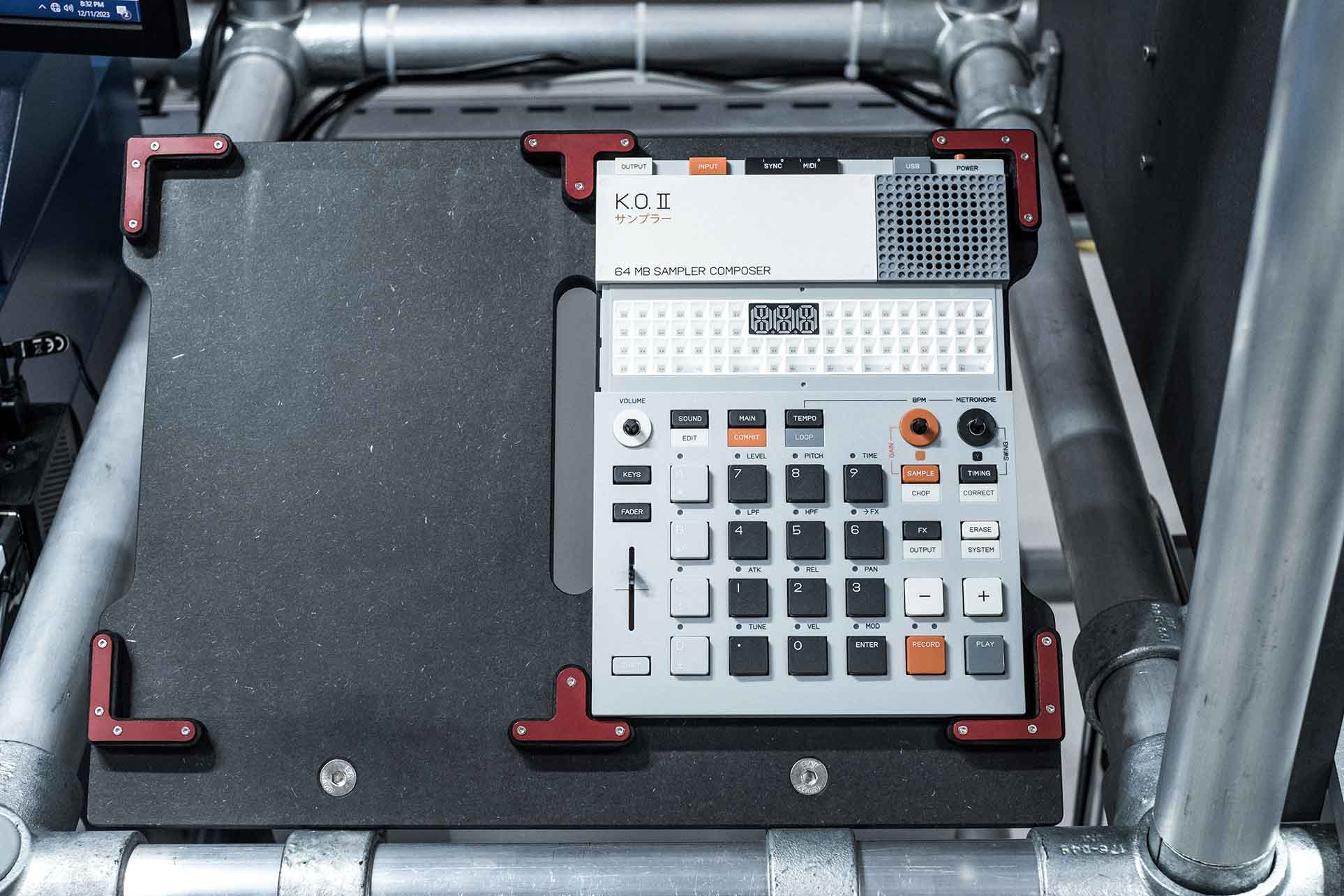
It’s a Knockout
Teenage Engineering, or TE, is known for quirky designs that are at once totally out there and nothing like anything else available but also exquisitely functional. TE partners with other companies, like IKEA (to make speakers), or the software company Panic (to make its PlayDate games console), but it is best known for its musical instruments, which often become extensions of their users. If the designs click with you, then you will fall for them, hard.
The company often gets compared to Apple, in terms of its opinionated, focus-group-free products, and its love of designing and building custom parts with unusual materials. For example, the OP-1 Field synth and sampler has the fit and finish of an iPhone Pro, and its cute-but powerful OP-Z sequencer uses magnetic hall-effect knobs on bearings for its controls, and mixes glass fiber into its injection-molded case. The company does not publish its own repair guides, but it does sell spare parts for the OP-1 and OP-Z through iFixit’s store and links to our repair guides from its site.
But during the pandemic, TE was faced, like everybody else, with long waiting times and chronic parts shortages. “It was so hard,” says David. “The lead time for parts was like one and a half to two years.”
The team instead tried to source off-the-shelf parts, in big enough numbers to keep a production line running. And once they had those parts in hand, they set about seeing what they could make.
The result is the EP-133 sampler, or K.O. II, named in homage to TE’s PO-33 K.O! Pocket Operator. It’s bigger than you might think from the photos, uses a neat, Game-&-Watch-style segmented LED display, and proves that you don’t need lots of custom parts to make something unique. Those number buttons, for example, are used for sampling, but also for playback, and while they have standard mechanical mechanisms, the team put a pressure sensor under the lower edge of each, making the keys velocity sensitive for more expressive playing.
Using off-the-shelf parts is also good news for repairability. In theory, the end user can also get access to those same parts, and in order to provide spares, the manufacturer just has to order extras and make them available to buy.
But the EP-133 is just half the story. “We probably spent way more hours on the production line than the actual development of the unit,” says David.
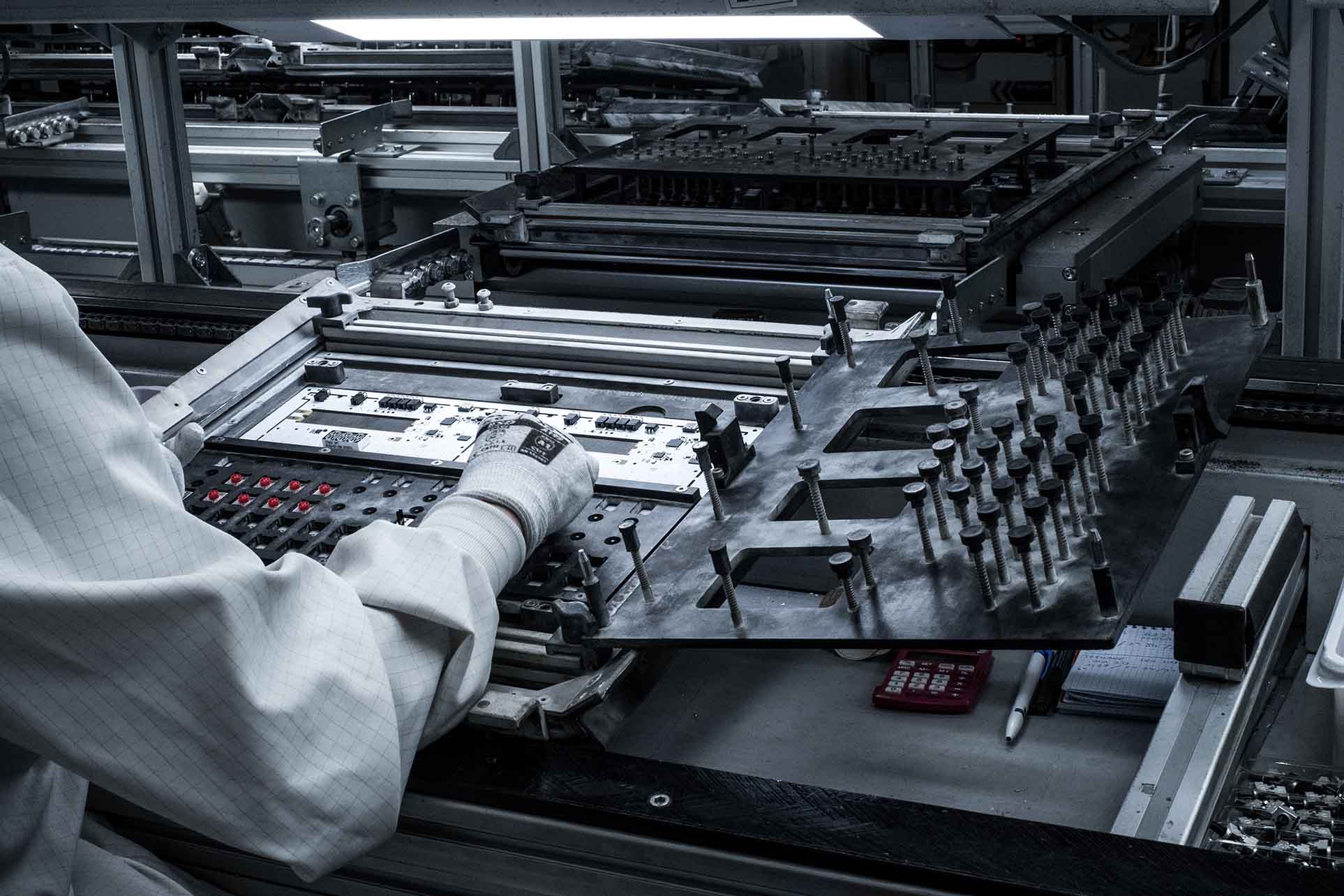
Factory
Having a production line close to home was important. Before settling on a facility in Barcelona, TE looked at 14 factories around Europe, including Lithuania, Estonia, Poland, France, Italy, Germany, and the Czech Republic.
“Some had really nice websites and presentations but when you went there, it was just so messy, dusty, no clean rooms, and, you know, paper-based warehouse systems,” says David.
And paper wouldn’t cut it. TE’s production line is seriously connected. It uses “AI cameras” over various stations to detect problems with assembly as they happen. If anything doesn’t look right, an alarm alerts TE immediately so they can correct the error, at that moment.
Teenage Engineering actually has two versions of its production line. One in the Barcelona factory, and one in its office in Stockholm. The Stockholm one doesn’t manufacture anything. It’s there so the team can design and test updates to the production process, both hardware and software, before uploading that software to the factory.
Testing is also automated, although that doesn’t always go to plan. For example, the speakers are tested by playing a frequency sweep that is recorded and analyzed to make sure it sounds right. Once, in the middle of the night, the factory called TE to report that all the speakers were failing their sound test. The system uploads these tests, and when the team back in Sweden listened, “it sounded like a helicopter was in the background on all the sweeps.”
The culprit? Somebody had put an automatic, rotary screw-sorting machine on the same table as the test device.
Teenage Engineering has more experience than most at manufacturing, and partners with other companies as well as making their own stuff. But this human-based glitch shows that no matter how experienced you are, even the best-thought-out plans rarely survive contact with the real world…
Fadergate
The launch of the K.O. II was a dream. It dropped with no pre-announcements, no YouTube synthfluencer videos, and—amazingly—no leaks, and was an immediate hit. Even usually-skeptical social media and electronic musicians’ forums loved it, especially at such a good price (it’s $350). But then, when people got them in their hands, there were two sometimes-recurring problems out of the box.
One was that the speakers didn’t work. People assembling this part should be wearing gloves, but as you can imagine, that doesn’t always happen. The result was contaminated connections. These can easily be fixed by opening up the case and cleaning the contacts, but David says that there is now a camera on that assembly line section to make sure it doesn’t happen again.
The other problem was the fader (one of the few custom parts), which is used to control effects, and all kinds of other parameters. It, too, was arriving DOA. User forums quickly diagnosed the cause. Marks on the inside of the box showed that it had been pressing down on the fader, and opening up the K.O. II showed that the electrical contacts inside were bent. Another easy fix, but still.
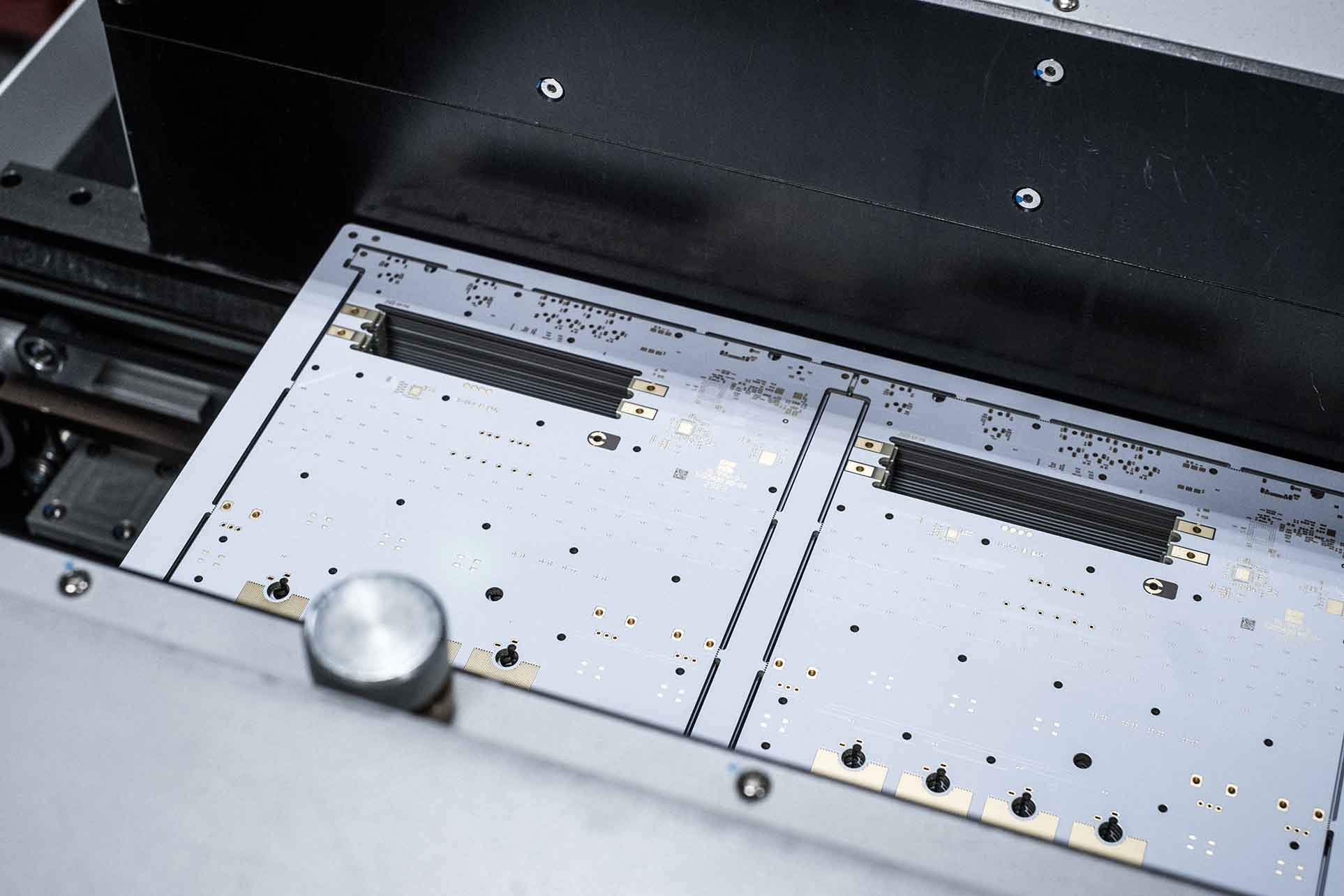
The problem here, says David, is that the units are packaged in thin display boxes, not shipping boxes. According to stories on forums, retailers have shipped them either loose inside other boxes, or naked. TE has already redesigned this packaging to help the fader survive1-meter drops. In the meantime, David himself took to the Elektronauts forum, run by fellow Swedish electronic musical instrument company Elektron, to help out users suffering these problems, although at that stage the community had already worked out that they just needed to clean the speaker contacts or bend the damaged pins back into place to repair the fader.
This level of communication is unusual in the gadget industry, and David actually brought up the fader problems before I could ask him about it. If anything, he seemed more upset by it than most of the users.
Repairability
While not designed specifically for repairability, the EP-133 is nonetheless easy to work on. It’s put together with screws (lots of screws, says David), with no pull-tabs or glued-in parts. It also uses AAA batteries instead of built-in lithium-ion batteries.
“Triple-As will work 10 or 20 years from now,” says David. “I mean, those batteries will exist, I’m sure. Whereas the lithium battery won’t.”
The unit itself is also designed for longevity. All those screws put in by a screw robot at the factory) make for a more rigid case, and some usually weak points are reinforced. The little colored plastic rectangles that surround the inputs and outputs on the top edge are not just there to look nice. Well, they are, but they also clamp around the jack sockets. The sockets are surface mounted, and these clamps help prevent them from snapping off the board with routing wear and tear.
The other side of designing things to last is the software, and TE has a good record in that department. The original OP-1 synth has received regular and significant updates throughout its life, including the addition of audio-over-USB (yes, via a software update) after ten years.
David also tells me that if and when spare parts for the EP-133 are made available, they will be made available to customers through the iFixit store.
It’s easy to take a look at a gadget and see only the end product, but the sleek exterior conceals a much messier design process. Designing for repair and longevity takes serious planning from engineers and executives, and it requires an ongoing commitment to iterating when unforeseen issues throw a wrench in the works. At the end of it all, though, the resulting product can be as beautiful and functional as it is repairable.
All photos courtesy of Teenage Engineering.
2 Comments
Can you please get the op-z keyboard replacement part? The cost for a repair (from TE's us repair partner) is the same as the cost for a complete replacement.
Kingof “kingof9x” 9x - Reply
lol they might want to consider sacking the AI in charge of catching defaults. Thing is riddled with them. Just look on Reddit and you’ll see fadergate, speaker issues, gaps in the side, possibly more.
Either that or they need to replace the battery in the alarm system as it’s not being heard. But then again TE are not listening to customer complaints and making any clear statements on these issues. So likely the Ai is for the chop.
Adam Casey (Ad Casey) - Reply